Selecting a Brushless DC Motor or Gearmotor

July 31, 2019
1. Determine application specifications for your brushless DC (BLDC) motor.
Several factors should be considered before selecting the appropriate motor for an application. In addition to speed, torque and duty cycle requirements are other critical aspects—including the voltage and current capacities for your power supply; whether you'll be working with an open- or closed-loop system; and whether velocity, current, or position control is required. Additional information would include the axial and radial loads on the motor shaft, what storage and operating temperature ranges are required, and any other environmental conditions that should be considered.
2. Is your motion a fixed value or variable?
For an application with fixed speed and load, locate the corresponding point on the speed/ torque curve of the motor you are considering and be sure that it falls within the continuous operating range. If you are working with variable speeds and loads, you'll need to calculate RMS torque (Root-Mean-Square). RMS torque is a function of time, which varies over the course of the move profile:

"T" is the torque for a given time increment "t".
If the result falls within the continuous operating range of the motor, it should not overheat. Keep in mind that values close to the peak operating limits can only be sustained for two to three seconds (depending on the specifications of your motor and drive platforms). You'll also want to know your peak torque and maximum speed to be sure they both fall within the operating range of the motor.

3. Decide on what type of motor works best.
For relatively low-torque and high-speed applications, you can get away with using only a motor to drive your motion. Coupling your motor with a gearbox, the same motor would be capable of delivering higher torques at slower speeds. For example, the top drawing illustrates the speed/torque curve of the ElectroCraft RapidPower™ Xtreme RPX22-042 BLDC motor, delivering 42 mN-m of continuous torque at 9,000 rev/min, while the bottom illustrates the same motor that can deliver between 130 mN-m at about 2,300 rev/min or 2,500 mN-m at about 13 rev/min depending on if it is coupled with a one-, two-, three-, or four-stage planetary gearbox.
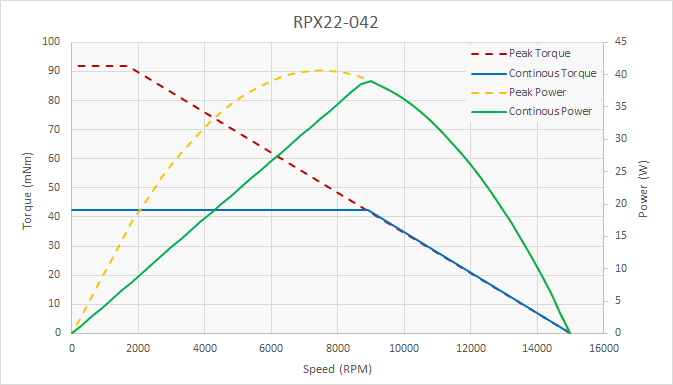
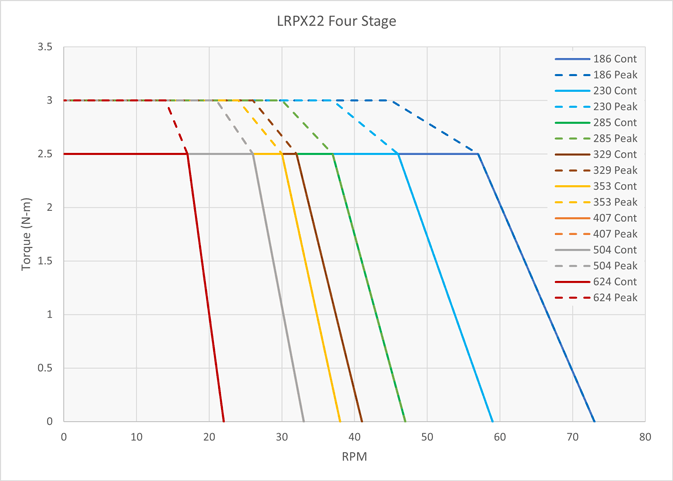
4. Know when a gearbox would be needed.

A gearbox matched with a BLDC motor is the right choice for your application if your torque requirement is higher than what your motor can deliver on its own, or if your system requires good dynamic response when there is a significant mismatch between rotor and load inertia (reflected inertia through a gearbox is 1/(reduction ratio)2. An added bonus to this scenario is that the motor will be turning faster than the output shaft, resulting in less velocity ripple.
An example of this approach that can reduce overall footprint might be to use an integrated planetary gearmotor, such as the ElectroCraft RapidPower™ Xtreme LRPX Series. It is important to remember that the motor-only or gearmotor decision should not be based solely on speed/torque requirements but also the type of motion control. For position control applications such as linear actuators, motor-only may be more desirable. For speed or current controlled applications, such as pumps or wheel drives, a gearmotor may be more desirable. Physical size, efficiency, cost, and power consumption all play a part in the decision, in addition to the reasons mentioned above.
5. Know how to connect your motor to the drive.

Most applications using BLDC motor drives require feedback to correctly sequence the current in the motor phases. Motors that come with feedback, such as a Hall effect sensor or incremental encoder, are an ideal choice. In this way a digital driver/controller can be used in current, velocity, or position control modes. Drives can use Hall effect sensors for trapezoidal commutation; some drives can also use these sensors for interpolated sinusoidal commutation.
Alternatively, an encoder can be added for more precise sinusoidal commutation. If the Hall effect sensor signals are used for velocity loop feedback, there could be significant velocity ripple at slow speeds. In this case, an encoder would provide more resolution, delivering better slow-speed performance. In position control mode for a BLDC motor, an encoder is necessary. ElectroCraft's CompletePower™ Plus – Universal Drive provides all of the above control methods for any DC motor type, in a single compact package.
Often design engineers are not motion specialists, in which case contacting the motor (or motor and gearbox) manufacturer can be a wise choice. Once you understand your application needs and are close to making a final decision, contact the manufacturer to hone your needs to your specific application. Their staff has the long-term experience and expertise with a wide variety of applications and can often help in those final stages.